本文已被:浏览 712次 下载 0次 |
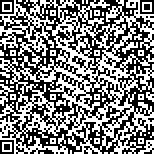 码上扫一扫! |
|
船用燃气轮机动力涡轮气动设计及优化研究 |
李翔宇1,2,霍玉鑫1,2,徐海成3,刘宇1,2,李国强1,2,牛夕莹1,2,朱晓明1,2,李越1,2
|
1.中国船舶集团有限公司第七〇三研究所,黑龙江 哈尔滨 150078;2.船舶与海洋工程动力系统国家工程实验室-海洋工程燃气轮机实验室,黑龙江 哈尔滨 150078;3.海军装备部装备项目管理中心,北京 100001
|
|
摘要: |
船用燃气轮机动力涡轮在大范围变工况下性能衰减严重,为满足动力涡轮宽工况气动设计的技术要求,本文基于某型船用燃气轮机热力循环参数,开展动力涡轮气动设计。通过正交实验法研究了涡轮效率对载荷系数等七个关键设计参数的敏感性;集成NREC软件内部模块,开展了一维优化设计;分别利用自由涡设计方法、可控涡设计与后加载叶型相结合方法进行了三维气动设计与优化。结果表明:涡轮效率对七个设计参数敏感性由高到低依次为平均流量系数、平均载荷系数、稠度、尾缘厚度与喉部宽度比值、反动度、叶顶间隙与叶高比值、展弦比;通过一维与两版三维气动方案结果对比与校核,涡轮在设计与低速工况下都具有良好的气动性能,说明形成的一维优化设计方法行之有效;采用可控涡设计和后加载叶型后,设计工况下总效率提高了0.62%,压比为2和6的低速工况下,总效率分别提高了0.764%和1.979%。可控涡设计相比自由涡设计而言,主要是对动叶降低损失,对径高比为5.1~7.8的涡轮级仍有一定的优化效果,在低速工况更明显。如配合静叶载荷形式的优化,效果更好。 |
关键词: 动力涡轮 敏感性分析 低维优化 可控涡设计 数值模拟 |
DOI:10.13675/j.cnki.tjjs.2203049 |
分类号:TK472 |
基金项目:国家科技重大专项(J2019-II-0009-0029);中船集团自立科技项目(202109Z);黑龙江省自然科学基金(TD2021E001)。 |
|
Aerodynamic Design and Optimization of Power Turbine for Marine Gas Turbine |
LI Xiang-yu1,2, HUO Yu-xin1,2, XU Hai-cheng3, LIU yu1,2, LI Guo-qiang1,2, NIU Xi-ying1,2, ZHU Xiao-ming1,2, LI yue1,2
|
1.No.703 Research Institute of CSSC,Harbin 150078,China;2.National Engineering Laboratory for Ship and Marine Engineering Power System- Marine Engineering Gas Turbine Laboratory,Harbin 150078,China;3.Equipment Program Management Center of Naval Armaments Department,Beijing 100001,China
|
Abstract: |
The performance degradation of marine gas turbine power turbine is serious under wide range of variable working conditions. In order to meet the technical requirements of aerodynamic design for power turbine under wide working conditions, the aerodynamic design of power turbine is carried out based on the thermodynamic cycle parameters of a certain marine gas turbine in this paper. The sensitivity of turbine efficiency to seven key design parameters such as load factor was studied by orthogonal experimental design. One-dimensional optimization design was carried out by integrating NREC software internal modules. Three-dimensional aerodynamic design and optimization were carried out by free vortex design method and a combination method of controlled vortex design and aft-loaded blade profile. The results indicate that the sensitivity of turbine efficiency to seven design parameters from high to low is average flow coefficient, average load factor, solidity, ratio of trailing edge thickness to throat width, reaction, ratio of tip clearance to blade height, and aspect ratio. By comparing and checking the results of one-dimensional and two versions of three-dimensional aerodynamic schemes, the turbine has good aerodynamic performance in both design and low speed conditions, which shows that the one-dimensional optimization design method is effective. With the controllable vortex design and aft-loaded blade profile, the total efficiency increased by 0.62% under the design condition, and the total efficiency increased by 0.764% and 1.979% under low-speed conditions with pressure ratio of 2 and 6 ,respectively. Compared with the free vortex design, the controlled vortex design method mainly has effect on reducing the loss of rotor blade, and still has a certain optimization effect on the turbine stage with the diameter-length ratio of 5.1~7.8, which is more obvious in low speed conditions. If combined with the optimization of stator type of loading, the effect is better. |
Key words: Power turbine Sensitivity analysis Low dimensional optimization Controlled vortex design Numerical simulation |