本文已被:浏览 1688次 下载 105次 |
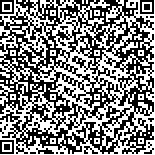 码上扫一扫! |
|
考虑编织损伤的2.5D编织 CMCs强度预测 |
孟维康1,2,张盛1,2,高希光1,2,宋迎东1,2,3,董洪年1,2
|
1.南京航空航天大学 能源与动力学院 航空发动机热环境与热结构工业和信息化部重点实验室,江苏 南京 210016;2.南京航空航天大学 能源与动力学院 江苏省航空动力系统重点实验室,江苏 南京 210016;3.南京航空航天大学 机械结构力学及控制国家重点实验室,江苏 南京 210016
|
|
摘要: |
通过测量SiC纤维束在受到不同曲率半径带来的弯曲损伤后剩余强度和弹性模量的大小,揭示曲率半径对SiC纤维性能的影响规律,考虑编织过程中的弯曲损伤对编织材料进行强度预测,以此指导复合材料编织工艺。对受到不同曲率半径的弯曲损伤后的SiC纤维束进行静态拉伸试验,将试验所得剩余强度和弹性模量与未受弯曲破坏纤维束强度进行对比。试验发现,弯曲损伤需要在曲率半径小于一定程度时才会对纤维束性能产生影响,纤维束弯曲曲率半径小于2mm后,弯曲损伤会随着曲率半径的减小而加大。基于试验结果,考虑2.5D织物结构特征计算发现板材厚度δ![]() 、纱线层数n![]() 和纬纱密度ρ![]() 等常用制造工艺参数满足nδ>2π2ρ2![]() 时,可得到强度良好的2.5D织物。借助有限元手段分析弯曲损伤对2.5D织物性能的影响,发现考虑纤维弯曲损伤后,2.5D编织复合材料的经向强度更低,断裂应变更大。 |
关键词: SiC纤维 曲率半径 剩余强度 弹性模量 弯曲损伤 纤维编织 |
DOI:10.13675/j.cnki.tjjs.210590 |
分类号:TB332 |
基金项目:国家科技重大专项(2017-IV-0005-0042);国家自然科学基金(51575261;51675266;11972183);中国博士后科学基金(2019M661834)。 |
|
Strength Prediction of 2.5D Braided CMCs Considering Braiding Damage |
MENG Wei-kang1,2, ZHANG Sheng1,2, GAO Xi-guang1,2, SONG Ying-dong1,2,3, DONG Hong-nian1,2
|
1.Key Laboratory of Aero-Engine Thermal Environment and Structure,Ministry of Industry and Information Technology,College of Energy and Power Engineering,Nanjing University of Aeronautics and Astronautics,Nanjing 210016,China;2.Jiangsu Province Key Laboratory of Aerospace Power System,College of Energy and Power Engineering, Nanjing University of Aeronautics and Astronautics,Nanjing 210016,China;3.State Key Laboratory of Mechanics and Control Mechanical Structures,Nanjing University of Aeronautics and Astronautics,Nanjing 210016,China
|
Abstract: |
By measuring the residual strength and elastic modulus of SiC fiber bundle after bending damage caused by different radius of curvature, the influence law of radius of curvature on the properties of SiC fiber is revealed, and the strength of braided material is predicted considering the bending damage in the braiding process, so as to guide the braiding process of composite material. A static tensile test was performed on the SiC fiber bundles that were damaged by bending with different radius of curvature, and the residual strength and elastic modulus obtained from the test were compared with the strength of the fiber bundles that were not damaged by bending. Tests have found that bending damage only affects the performance of the fiber bundle when the radius of curvature is less than a certain degree. After the bending radius of the fiber bundle is less than 2mm, the bending damage will increase as the radius of curvature decreases. Based on the test results, considering the structural characteristics of 2.5D fabrics, it is found that when the common manufacturing process parameters such as sheet thickness δ![]() , yarn layers n![]() and weft density ρ![]() meet nδ>2π2ρ2![]() , 2.5D fabrics with good strength can be obtained. The effects of bending damage on the properties of 2.5D fabrics were analyzed by means of finite element methods, and it was found that after considering fiber bending damage, the warp strength of 2.5D braided composites was lower and the fracture strain was larger. |
Key words: SiC fiber Radius of curvature Residual strength Elastic modulus Bending damage Fiber weaving |