本文已被:浏览 819次 下载 127次 |
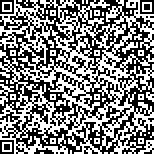 码上扫一扫! |
|
启动过程压缩空气储能向心涡轮三维流动特性研究 |
刘祖煜1,2,王星1,李文1,2,3,4,王强3,陈海生1,2,3,4,朱俊强1
|
1.中国科学院工程热物理研究所,北京 100190;2.中国科学院大学 工程科学学院,北京 100049;3.毕节高新技术产业开发区国家能源大规模物理储能技术研发中心,贵州 毕节 551700;4.中科院工程热物理研究所 南京未来能源系统研究院,江苏 南京 211135
|
|
摘要: |
为研究压缩空气储能系统的向心涡轮启动过程内部流动损失特性,采用全三维计算流体动力学(CFD)模型对其启动过程进行了数值模拟,与实验结果对比表明,虽然该模型在启动初始阶段与转速稳定阶段存在一定误差,但仍能够整体上反映启动过程的效率变化特征。在此基础上,进一步分析了启动过程中动叶通道内损失区及流场变化特征,结果发现,动叶进口攻角是影响内部流场主要因素:在启动初始阶段,叶轮进口攻角较大,动叶载荷集中在叶片前缘,形成明显的通道分离涡与前缘涡;在快速启动段,攻角减小,动叶载荷沿弦长分布更为均匀,通道分离涡及前缘涡逐渐减小并向叶片吸力面迁移。在整个启动阶段,动叶通道内高损失区也随着通道分离涡逐渐迁移且变小,并向相邻叶片吸力面集中。 |
关键词: 压缩空气储能 涡轮 启动 三维流场 变工况 |
DOI:10.13675/j.cnki.tjjs.201016 |
分类号:TK05 |
基金项目:国家重点研发计划(2017YFB0903602);国家杰出青年科学基金(51925604);中国科学院国际合作局国际伙伴计划(182211KYSB20170029);毕节市科技支撑计划项目(毕科合字[2017]13号)。 |
|
Three Dimensional Flow Characteristics of a Radial Inflow Turbine in Compressed Air Energy Storage System During Start-Up Process |
LIU Zu-yu1,2, WANG Xing1, LI Wen1,2,3,4, WANG Qiang3, CHEN Hai-sheng1,2,3,4, ZHU Jun-qiang1
|
1.Institute of Engineering Thermophysics,Chinese Academy of Sciences,Beijing 100190,China;2.School of Engineering Science,University of Chinese Academy of Sciences,Beijing 100049,China;3.Bijie High-Tech Industrial Development Zone National Energy Large Scale Physical Energy Storage Technologies R&D Center,Bijie 551700,China;4.Nanjing Institute of Future Energy Systems,Institute of Engineering Thermophysics, Chinese Academy of Sciences,Nanjing 211135,China
|
Abstract: |
To study the internal flow loss characteristics of the radial inflow turbine in Compressed Air Energy Storage (CAES) system during start-up process, a full three-dimensional Computational Fluid Dynamics (CFD) model was established to simulate the flow field of CAES radial turbine during start-up, and the results were also validated with the experiment. It can be found that the numerical simulation results of total-to-total efficiency are basically in well agreement with the experimental results in trend, although the deviation only occurs in the initial and stable speed stages of the start-up process. Furthermore, the loss area and flow structure in the rotor passage during start-up process were also analyzed. The results show that the rotor inlet angle of attack is the main factor affecting the internal flow field: in the initial start-up stage, higher rotor inlet angle of attack increases the blade load near the leading edge of the blade resulting in obvious passage separation vortex and leading edge vortices; in the fast start-up stage, the attack angle is decreased, and the distribution of the rotor load is more uniform along the chord length. The passage separation vortex and leading edge vortices thus gradually decrease and migrate to the suction surface of the blade. During the whole start-up process, the high loss area in the rotor passage is also reduced and gradually moves to the suction surface of adjacent blades with the passage separation vortex. |
Key words: Compressed air energy storage Turbine Start-up Three dimensional flow field Variable working conditions |