本文已被:浏览 1799次 下载 863次 |
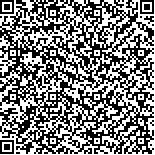 码上扫一扫! |
|
冲压发动机C/SiC喷管承压失效研究 |
李志永1,郑日恒1,李立翰1,刘小瀛2,赵东林2,陈博2,成来飞2,张立同2
|
(1.中国航天科工集团三十一研究所 高超声速冲压发动机技术重点实验室,北京 100074; ;2.西北工业大学 超高温结构复合材料重点实验室,陕西 西安 710072)
|
|
摘要: |
新型三维编织碳/碳化硅复合材料存在较强的各向异性,而各个方向的性能数据积累不足,复合材料的强度计算方法尚不完善,为了发现新型三维编织碳/碳化硅复合材料在冲压发动机喷管中应用可能遇到的问题,并找到相应地解决措施,开展了这种复合材料应用于冲压发动机喷管的承压强度计算和承压实验研究。对承压实验中出现的低压破坏情况进行了分析,分析了低压破裂的原因,提出了改进措施。分析结果表明:C/SiC喷管喉部密度较低,导致强度较低,承载能力下降,是首次强度验证实验过程中该局部破坏的原因;为提高喷管强度,需要通过其形状设计并控制沉积流场,保证其喉部的沉积密度达到1.9g/cm3以上。对改进后的喷管进行了实验验证,实验结果与计算结果基本一致,满足要求。因此,在实际应用中应对喷管喉部和纵向密度的分布进行工业CT无损检测,确保喷管密度的分布均匀。 |
关键词: 碳/碳化硅复合材料 冲压发动机 承压 失效分析 |
DOI: |
分类号: |
基金项目: |
|
Investigation on Bearing Failure of Ramjet C/SiC Nozzle |
LI Zhi-yong1, ZHENG Ri-heng1, LI Li-han1, LIU Xiao-ying2,ZHAO Dong-lin2,CHEN Bo2,CHENG Lai-fei2,ZHANG Li-tong2
|
(1.Science and Technology on Scramjet Laboratory,The 31st Research Institute of CASIC,Beijing 100074,China; 2.Science and Technology on Thermostructural Composite Materials Laboratory,Northwestern Polytechnical University, Xi’an 710072,China)
|
Abstract: |
The strong anisotropy of the 3D braided C/SiC composite materials exists.In addition, Property data in each direction is insufficiently accumulated and the composite strength prediction method has not been well developed. In order to identify problems in the application of ramjet nozzle made of the 3D braided C/SiC composite material, and to find the corresponding solutions, strength prediction and experimental research were carried out for the ramjet nozzle. Composite nozzles ruptured under low pressures in the pressure test were analyzed so as to find reasons and solutions for the early failure. The results showed that the C/SiC nozzle throat was of low density, resulting in low strength and weak bearing capability, which was the local destruction reason for the first strength verification test. In order to improve the strength of the nozzle, it needs to be ensured that the throat deposition density should be above 1.9g/cm3by design and control of the deposition flow field parameters according to the geometry of the nozzle. The improved nozzle was verified by the experiment.The experimental and the calculation results were basically consistent,and it meets the requirements. To ensure the even distribution of the nozzle density, density distribution of the nozzle throat and longitudinal directions should be non-destructively tested using industry CT. |
Key words: C/SiC composite Ramjet Bearing pressure Failure analysis |