本文已被:浏览 879次 下载 560次 |
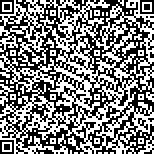 码上扫一扫! |
|
旋流杯结构及进气参数对燃烧性能的影响 |
姜磊1,2,熊健3,肖波1,2,王博涵1,2,胡宏斌1,2
|
1.中国科学院工程热物理研究所 先进燃气轮机实验室,北京100190;2.中国科学院大学,北京100049;3.中国航发贵州黎阳航空动力有限公司,贵州贵阳550014
|
|
摘要: |
为优化旋流燃烧室头部结构、提高其运行性能,针对三种旋流器文氏管和燃料喷嘴的组合结构和两种流通面积的旋流器,开展了常压下以甲烷为燃料的燃烧室性能实验研究。实验结果表明,各头部结构的冷态总压损失系数与来流速度的平方成正比,燃料喷嘴插入文氏管的位置过深或过浅都会增大流动阻力,在来流速度9.7m/s条件下,喷嘴处于中等插入位置时总压损失系数降低6%左右;开放空间下,燃料喷嘴的位置越浅越利于火焰稳定,受限条件下这种影响被缩小,并且受限火焰的稳定工作范围明显宽于相同入口条件下的开放火焰;增大旋流器流通面积有利于降低总压损失系数、增强火焰稳定、减轻火焰筒壁面振动幅度,但不利于促进燃料和空气掺混,导致NO和CO的排放浓度都变大;在临近贫油熄火状态时,火焰筒壁面振动幅度加剧,明显高于稳定燃烧时的情况。 |
关键词: 旋流器文氏管 燃料喷嘴 燃烧室 总压损失系数 贫油点火极限 贫油熄火极限 流场 |
DOI:10.13675/j.cnki.tjjs.190199 |
分类号:V231.2 |
基金项目: |
|
Effects of Swirl Cup Structure and Inlet Parameters on Combustion Characteristics |
JIANG Lei1,2,XIONG Jian3,XIAO Bo1,2,WANG Bo-han1,2,HU Hong-bin1,2
|
1.Advanced Gas Turbine Laboratory,Institute of Engineering Thermophysics, Chinese Academy of Sciences,Beijing100190,China;2.University of Chinese Academy of Sciences,Beijing100049,China;3.AECC Guizhou Liyang Aviation Power Co. Ltd.,Guiyang550014,China
|
Abstract: |
In order to optimize the head structure of swirl combustor and improve its performance, the experimental study on the performance of methane-fueled combustor under normal pressure was conducted based on the three combined structures of swirler venturi tube and fuel nozzle, as well as two swirlers with different flow areas. The experimental results show that the cold total pressure loss coefficient of each head structure is proportional to the square of inlet airflow velocity. The flow resistance becomes larger when the position of the fuel nozzle inserted into venture is either too deep or too shallow. In the case of the inflow velocity of 9.7m/s and intermediate insertion length, the total pressure loss coefficient decreases by approximately 6%. Under unconfined condition, the shallower the position of fuel nozzle is,the better the flame stability will be. However, this effect on flame stability would be reduced upon confinement, and the stable working range of the restricted flame is obviously wider than that of the open flame under the same inlet condition. Increasing the swirler flow area would be beneficial to reduce the total pressure loss coefficient, enhance the flame stability and relieve the vibration amplitude of the flame cylinder wall, but it is not conducive to promoting the mixing of fuel and air, resulting in higher emission concentrations of NO and CO. When the combustor operates near lean flameout, the vibration amplitude of the wall increases, which is enormously higher than that of stable flame with rich fuel. |
Key words: |